Spray Nozzles For Descaling
Spray Technology For the Steel Industry
Spray Nozzles For Descaling
Removing scale prior to rolling is critical for product quality and finish, rolled in scale from hot strip mills or mini mills is detrimental to the steel quality.
Using high pressure water of up to 400 bar (5800 psi) and specially designed descaling spray nozzles made of stainless steel with tungsten carbide inserts creates the maximum uniform impact onto the steel using the minimum volumes of water.
Specifying the correct nozzle type and arrangement is absolutely critical when designing a new or looking to improve an existing descaling as there are a number of factors that are needed to be taken into account:
Impact & Erosion Force:
In order to achieve best steel surface quality, specially designed flat fan nozzles are used remove the oxide scale from the surface of the steel product. These nozzles are designed in a way which maximises the impact the formed spray has on the surface, this is achieved through specially designed internals as well as the use of high-quality tungsten carbide tip inserts which allow for greater pressure to be used and increase the life of the nozzle. To aid control of the spray pattern, filter stabilisers are also used within the nozzle assembly, they play a key role in removing any particles the descaling systems filtration systems haven’t picked up while also giving the descaling nozzle a much more stable spray, which results in higher, more efficient impacts and erosion force.
Specifying the correct nozzle type and arrangement is absolutely critical when designing a new or looking to improve an existing descaling as there are a number of factors that are needed to be taken into account:
Distribution:
When descaling a steel product, it is important to have the correct distribution of the spray when designing the nozzle layout and spray headers. As multiple nozzles are needed to evenly cover the material surface, careful consideration is needed in terms of stand-off height from the nozzles to the steel, spacing between each nozzle and the angle to which the nozzles are offset from each other.
As the water pressure is so high in descaling systems, any interference between the sprays can have a detrimental effect on the surface quality. This is also the case if the descale nozzle arrangement is not designed properly, for example if the there are gaps between the sprays, then the end result can be striping on the steel.
Sealpump can help eliminate these issues by working with steel mills and equipment manufacturers to make sure the descale spray system is correctly laid out.
Flow Rate & Pressure:
With the aim of producing the best possible surface finish, pressure and flow rate are the two biggest factors in the design of a descaling spray system, however, they are also the two biggest factors when it comes to running cost. Therefore, achieving a balance of high impact with as low a flow rate as possible at a lowest pressure as possible is very important for many steel mills, especially due to the increasing energy costs.
New nozzle technology means that by changing outdated descaling spray nozzles for new technology, less water and less pressure can be used, whilst also improving scale removal and surface quality. This means steel mills can reduce the electrical energy bills by reducing the descaling pump pressure and reduce the amount of water the mill uses.
We offer a wide range of descaling spray nozzles with various flow rate and spray angle options. In addition we can help with nozzle layout and with the design and supply of descaling spray headers.
Sealpump sales engineers will assist in helping size the correct spray nozzles and offer competitive pricing and availability, please contact our office for further details.
Removing scale prior to rolling is critical for product quality and finish, rolled in scale from hot strip mills or mini mills is detrimental to the steel quality.
Using high pressure water of up to 400 bar (5800 psi) and specially designed descaling spray nozzles made of stainless steel with tungsten carbide inserts creates the maximum uniform impact onto the steel using the minimum volumes of water.
Specifying the correct nozzle type and arrangement is absolutely critical when designing a new or looking to improve an existing descaling as there are a number of factors that are needed to be taken into account:
For Technical Information and Specifications,
download our PDF
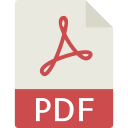