Humidification for Packaging
Humidity Control for Packaging Materials
Controlling Humidity for Packaging
Nearly all products we buy, or manufacture are bought and shipped out in a form of packaging to protect the product inside and also as a way of advertising the company whose item it is, while also trying to ensure the design and makeup of the packaging as environmentally friendly as possible.
Much like in the printing industry, achieving and maintaining the correct humidity level is essential in maintaining product quality and production speed and efficiency. Whether in the manufacturing process of cardboard for boxes or inserts, embossed board or paper or label printing, low humidity has a detrimental effect on the production process and the finished product.
Across the many different types of packaging manufacture, generally a humidity level of 50-60% rh in recommended to provide the air the moisture it needs to allow the material & equipment used to work at optimal levels with the least amount of product waste and needless machine downtime.
Problems caused by low humidity in the packaging industry
- Paper Storage – When paper or cardboard is stored in dry conditions, it can lose moisture and therefore lose shape and becomes difficult to process. This can lead to problems further in production such as splitting and the creation of static electricity.
- Carton & cardboard – Cracking can occur on the external face of the folds due to low moisture content caused by low humidity.
- Label Printing – this is susceptible to low humidity for numerous reasons. Low humidity can cause the paper to dry and curl and lose its shape, making it hard to process and handle. This can then create static electricity which makes processing hard. The expensive ink used can also dry out meaning it is replaced more often with a lot of waste and avoidable downtime.
- Gluing – Moisture can be drawn from the adhesives used to either stick labels on card, glass or cans or to glue parts of packaging together, which reduces the effectiveness of the glue. Adding humidification back in, solves these issues.
- Embossing Process – Cracking or tearing can occur during this process especially on areas where the card or paper has been made thinner.
ADVANTAGES
Rapid investment payback
Dry Fog or Micro Drop Technology
Low maintenance
Low energy & running costs
Hygienic design
User friendly controls
Highly efficient humidification
95% cost saving compared to steam humidification
For Technical Information and Specifications,
download our PDF
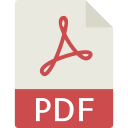
Related Products and Pages