Dust Suppression Theory and Application
Sealpump, Spray Technology Experts
How Do Dust Control Systems Work?
Dry Fog fugitive dust suppression works like a combination of a wet scrubber and a fabric filter. The generated ultra-fine fogging blanket acts like a fabric filter in that a dust particle cannot pass through it without colliding with a droplet. Since the droplet consists of water, the dust particle does become somewhat wet as in a true flooded scrubber. This phenomenon can be called agglomeration. Solving fugitive dust emission problems using ultra-fine water droplet atomisation begins with the theory of agglomeration. Agglomeration can be defined as the gathering of mass into a larger mass, or cluster.
Agglomeration probability is greatly increased between bodies of similar size. The agglomeration of these bodies produces a large enough mass to cause settling. For example, a dust particle of 5 microns will continue to follow the air stream around a water droplet of 200 microns, therefore, avoiding collision. With the dust particle and a water droplet of similar size, the air stream is not as great and collision occurs, causing agglomeration.
The diagram below shows the aerodynamics of what can happen when the water droplets are larger than the dust particle.
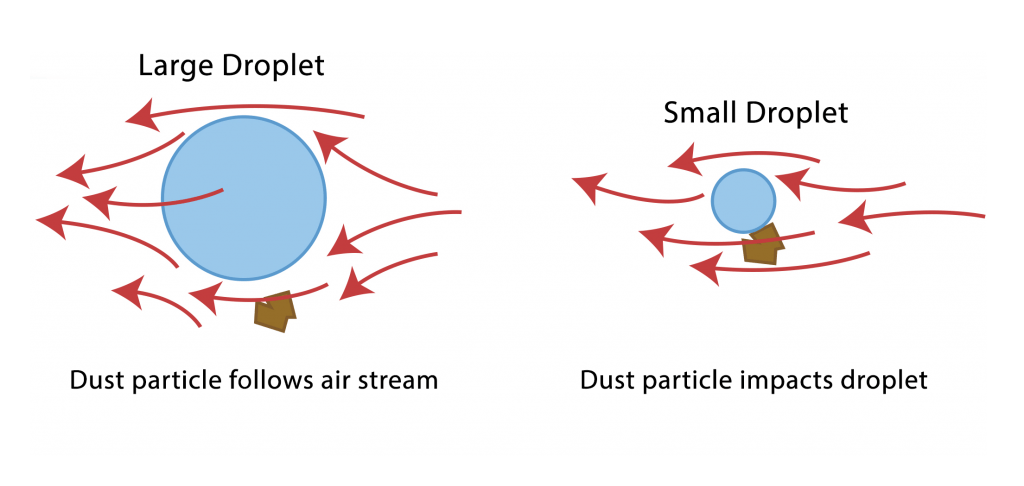
Diagram illustrates the importance of droplet size for particle agglomeration. Airflow around the large water droplet (left) prevents the dust from contacting the droplet. However, the dust particle easily impacts the small droplet (right) triggering agglomeration.
Fog suppression is one method to optimise the application of water to dusty materials. These systems use special ultrasonic nozzles to produce extremely small water droplets (10 microns or less) in a dispersed mist. These droplets mix and agglomerate with dust particles of similar size, with the resulting larger combined particles falling back to the material body.
Dry Fog Dust Suppression Systems control virtually all types of less than 5 micron breathable as well as larger size fugitive dust up to 600 microns. Control is accomplished through agglomeration of ultrasonically produced water droplets equal or close to the size of the dust particles. These include silica sand, dried clay, dry sand, limestone, aggregate, road stone, phosphate, coal, quartz, fibreglass and many others. The Dry Fog system suppresses visible emissions from primary and secondary crushing, screening, transfer and loading-unloading facilities such as hoppers, feeders, bins, docks, silos, terminals and vehicles.
The sonicom atomising nozzle along with a compressed air supply and simple on/off controls will suppress respirable dust as small as 0.1 to 3 microns as well as larger size particles. The initial cost, operation and maintenance of a Dry Fog System is much lower than a ventilation type control system. In contrast to the use of large ducts and related equipment, the sonicom system operates with smaller diameter tubing on as little as 5% of the total energy of conventional systems. Dry Fog systems can be installed for as little as 40% of the installation cost of a conventional bag filter type system.
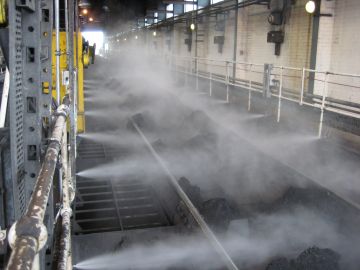
They offer the following advantages:
water consumption averages 20 litres per hour per nozzle
nozzles operate on low air and water pressures to eliminate need for pumping systems
air consumption approximately 4.72 lt/sec (10 scfm) per nozzle
water addition to process, less than 0.1%
costly wetting agents and their controls eliminated
water source and disposal problems eliminated
needs no significant modifications to existing plant for installation
low maintenance
nozzles are self-cleaning
airborne water freezing avoided by producing same size droplets found in clouds
Basic research in the development of the sonicom Dry Fog Dust Suppression System showed that if a sufficient number of water droplets of approximately the same size as the dust particles could be produced, the possibility of collision between the two would be extremely high. It was also determined that if the droplet exceeded the size of the dust particle, there was little probability of impact and the desired precipitation. Instead, the dust particle would move around the droplet.
The sonicom nozzle assembly is ideally suited for generating a dense fog of ultra fine droplets to envelop and bring down the dust particles at their source. By controlling air pressure, atomisation quality can be varied from course – 200 microns – to an ultra-fine fog of 1 to 10 microns. When the nozzle is complemented with our special water valve assembly, the unit becomes a highly efficient self cleaning atomiser
The heavy duty stainless steel water valve is controlled by the same compressed air supply used to activate the nozzle. A simple on/off signal is required to activate the system and when the signal is removed, the water valve self cleans the nozzle every time by blowing excess water away, significantly reducing lime, salts and chalk build-up.
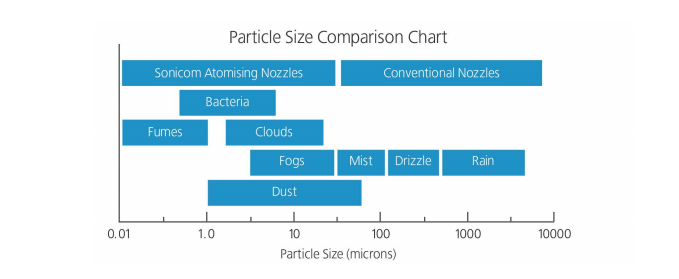
The “œdry fog” dust suppression system controls respirable particulates down to the 0.1 to 3 microns which are considered to be the principal source of dust clouds, haze and accompanying low levels of visibility. In most applications where respirable dust particles can be settled out of the atmosphere quickly, the sonicom system makes it unnecessary to add a tension additive product to the water.
Total water consumption is extremely low – only 0.1% of production at each point of concern (less than 0.5% of that consumed by conventional sprays) ensuring that conveyor belt wetting and other accompanying tracking problems are avoided. Control of water output is achieved by simple pressure control. The volume of water can be modified in relation to the humidity content of the pulverised silica. The sonicom system also provides these benefits:
less product wetting than conventional water spray systems (less than 0.5%)
micron size water droplets multiply surface area while decreasing total water needed
costly wetting agents and their controls eliminated.
no conveyor belt wetting or accompanying tracking problems
less conveyor downtime and fewer conveyor belt replacement parts
agglomeration of dust helps improve performance of precipitators, baghouses and collectors
nozzles operate on low pressure air and water to eliminate need for expensive pumping systems
improved working conditions enables compliance with applicable health and safety regulations
cleaning and maintenance costs reduced
permits recovery of spilled materials
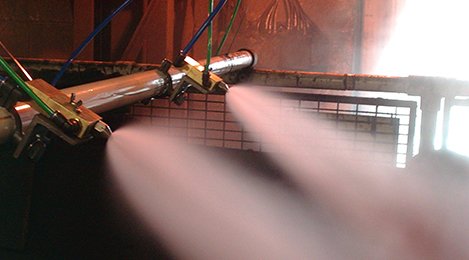
The Thermal Penalty for Added Moisture
There is a substantial performance penalty added to combustion and other thermal processes when the water content of the fuel is increased. In applications like coal-fired power plants and cement plants, water added to the material going into the thermal process must be “œburned off” by the process. This can dramatically reduce the process efficiency and increase fuel costs
It requires 3,064 kilojoules per litre (1,320 BTU per pound) to raise water from 21°C (70°F) to it”™s vaporisation temperature of 149°C (300°F). It only takes 9.1 kg or 9.1 litres (20 pounds) of water to increase the moisture content of one tonne of material by one percent. As a gallon of water weighs approximately 4.5 kg (10 pounds), the addition of less than 2.0 gallons (9.1 litres) of water to a tonnne of material will raise the moisture content of a tonnne of material by 1 percent. Vaporizing this modest amount of water produces a heat loss of 27,850 kilojoules (26,400 BTU).
The thermal penalty typically created by the various dust suppression methods is displayed below.
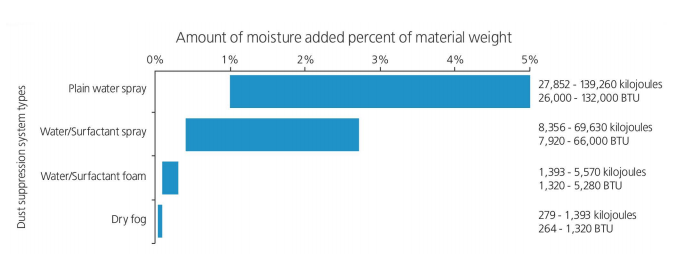
Because a “œplain” water spray requires the highest volume of moisture for effective dust suppression, this method extracts the highest thermal penalty. While the use of a simple water spray for dust suppression may be a lower cost because the water is readily available and there is less “œout-of-pocket” expense, the penalty for the addition of surplus moisture can be very costly indeed.
Principle of Ultrasonic Nozzle
Compressed air passes through the nozzle’s inner bore through a convergent/divergent section at high velocities and expands into a resonator cavity where it is reflected back to complement and amplify the primary shock wave. The result is an intensified field of sonic energy focused between the nozzle body and the resonator cap.
Any liquid capable of being pumped into the shock wave is vigorously sheared into fine droplets by the acoustic field. Air bypassing the resonator carries the atomised droplets downstream in a soft plume shaped spray.
The droplets have low mass and low forward velocity with low impingement characteristics. Fine atomisation ensures uniform distribution of the liquid with minimum over spray and waste.
Ultrasonic atomising nozzles operate at very low liquid pressures and have large orifices. The large orifices and low pressures virtually eliminate orifice wear and prevent deterioration of the quality of atomisation while greatly extending useful nozzle life.
The plume leaving the fog system nozzles is so fine it will not freeze, but the water supply system itself can freeze if drain or heating elements are not provided.
Sonicom Ultrasonic Fogging Nozzle
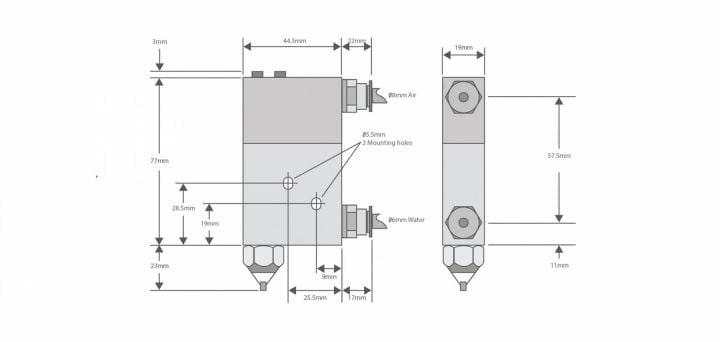
Description:
The sonicom ultrasonic atomising nozzle shatters liquid into micron size droplets ranging from 20µm down to 1µm and less by means of a compressed air supply at 5 Bar (75psi) and liquid supply at 1 Bar (15psi).
When assembled with it’s own unique stainless steel water valve, the nozzle assembly becomes non-drip, is self cleaning after every operation and reduces control requirements to a simple on/off air supply. The same air supply is used to control the valve and activate the nozzle atomisation.
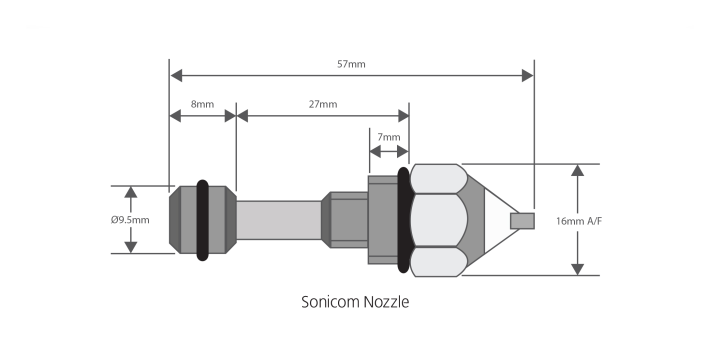
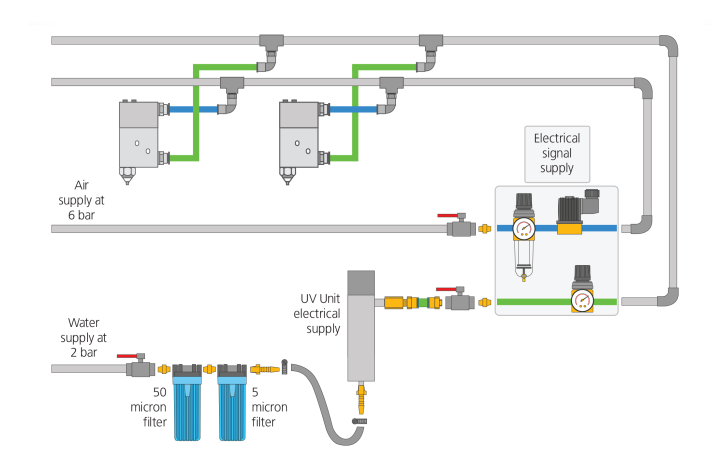
Application
- Smaller water droplets
- Mains water pressure – no pump required
- Minimal water consumption
- Simple to install
- Low pressures
- Range of nozzle sizes
- Self cleaning every cycle
- Range of nozzle sizes
- Each nozzle fitted with nondrip valve
- Easy to operate
- Large liquid ports – prevents clogging
- Reduced wear and maintenance
- Consistent quality of atomisation
Materials Available
- Nozzle Head: Stainless Steel
- Water Valve: Stainless Steel
- Internal Seals: Viton
- Temperature Range: -20° to +180°C
For More Information on Dust Suppression, download ….
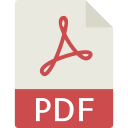