Humidity Control for the Print Industry
Sealpump, Experts in Humidification Systems
Humidity Control for Printing
It is essential to create and maintain the correct process conditions within the print industries various stages of production and controlling the humidity level is vital.
There are several problems that low humidity can have in the print industry, all of which have a negative effect on the manufacturing process, materials being used and ultimately the finished product.
Paper curl, cracking during folding and cutting, static electricity and airborne dust are all problems caused by dry air in the printing process. Introducing humidification into the workplace solves such quality problems, protects expensive equipment, stops inks drying out and creates a much more comfortable work environment.
Another important factor in selecting the most appropriate humidification system for printing applications is the right type of water treatment. While water filtration and ultraviolet disinfection is important in any humidification system to both protect the people in the room and protect the humidity system and nozzles, in industries such as printing their cannot be any residue such as calcium in the water as this can settle on the print machines or products. In these industries, we then also install reverse osmosis water treatment and sometimes water softeners (depending on location and water quality).
Whatever the type of printing application, whether it is small scale or large scale, digital or web printing, we work with our customers to create a perfectly tailored, efficient, low maintenance humidification system.
EFFECTS ON PAPER:
Low humidity can have a dramatic effect on the properties of paper as it is hygroscopic and loses a lot of moisture content when being stored or processed in dry conditions, therefore controlling the air to the correct humidity is extremely beneficial.
Should the humidity fall below 50-55%, moisture begins to be drawn from the paper which leads to the paper drying out and losing its shape and consistency.
Further reduction in humidity, caused by dry air and the heat generated by the process, will cause static build up, which in turn causes paper sheets to stick together, blocking the machine feed. This results in paper waste and expensive machine down time for maintenance.
EFFECTS ON INK:
Inks are an expensive & essential consumable in any printing operation so being able to use all the ink over a long period is critical. Low humidity can speed up the drying out of the ink used. This leads to more ink being used and replacing sooner which brings unnecessary costs and more production downtime. Controlling the humidity with a well-designed humidification system, combats this by providing the ambient air with the moisture it needs, therefore keeping the ink in the best condition. Typically, this is around 55-60%
EFFECTS ON DIGITAL PRINTING:
The effects of low humidity can be seen in the various stages of digital printing, from paper roll storage and processing where the paper loses moisture and shape, to static being created which makes handling and processing time consuming and difficult. To add to this, as digital printing requires high-tech printing machines, these machines generate heat and in turn more static, causing further issues, which can all be solved with the installation of a humidification system.
EFFECTS ON WEB PRINTING:
As web printing is generally used in high or mass production printing, any delay in production can have hugely expensive consequences. Web printing uses large rolls of paper which are fed through a printing press for continuous running. Therefore ensuring that the paper rolls are stored in the correct humidity reduces the risk of the paper losing form or creating static.
As the paper moves into the press, the edges of the roll are put under a lot of stress, meaning they can tear easily if they do not have enough moisture in them.
Maintaining the humidity at 50-60% around the press in the production hall will mitigate the creation of static electricity which can occur due to the speed of the paper as it is passed through the press.
All of the above issues can be drastically improved by the use of the correct humidification system.
For Technical Information and Specifications,
download our PDF
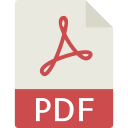