Dust Control for Conveyor Transfer Chutes
Sealpump, Spray Technology Experts
Dust Control for Conveyor Transfer Chutes
As specialists in dust suppression and control, Sealpump can solve all your Conveyor Transfer Chute dust problems.
The placement of the dry fog nozzles is the most important aspect to achieving effective dust suppression and ensuring no wetting of material, the dry fog spray should be generated and contained in well designed shrouding, for example a conveyor chute, this eliminates dissipation due to wind and also ensures treatment time necessary to suppress and control airborne dust.
The dry fog spray is generated above the dust problem area not directly onto the material, as the airborne dust is generated within the conveyor transfer chute the dry fog suppresses the dust through particle agglomeration, ensuring that the dust is controlled within the conveyor transfer chute.
A general rule of thumb is that the height of the conveyor cover be approximately 1 metre above the product level on the belt. And the cover length 3 times the belt speed (m/s).
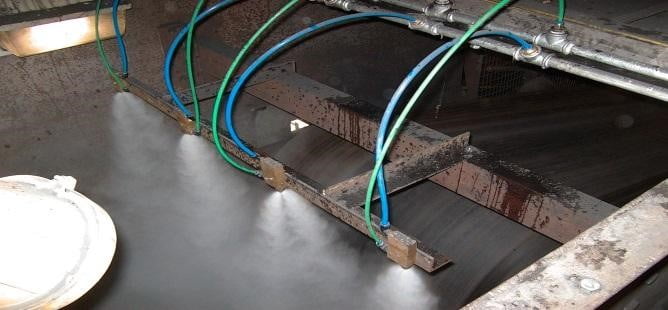
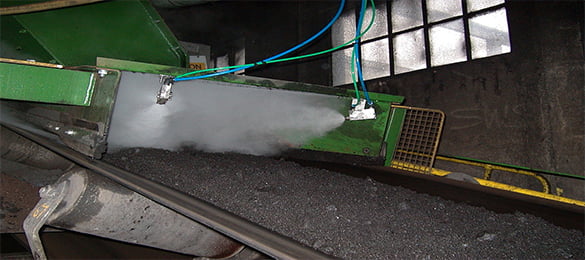
How Many Nozzles Are Needed?
There are several factors to consider when specifying the number of nozzles required at a given problem area:
- Tonnage per hour
- Type of material being conveyed
- Condition of material
- Future use of the material
- Crusher size / capacity
- Convenience of mounting space / maintenance
Locating The Nozzles
The basic principles involved for location of the nozzles are as follows:
- Nozzle spray pattern must not directly impinge upon any surface
- Nozzles should be mounted in order to maximize the ability to fill the shrouding
- Where possible the fog should avoid direct contact with the material being suppressed
- Nozzles must be protected or shielded to avoid damage from falling material
- Spray pattern of nozzles should be generated so that all the fugitive dust emissions are forced to pass through the blanket of fog
For Technical Information and Specifications,
download our PDF
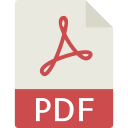